Summary
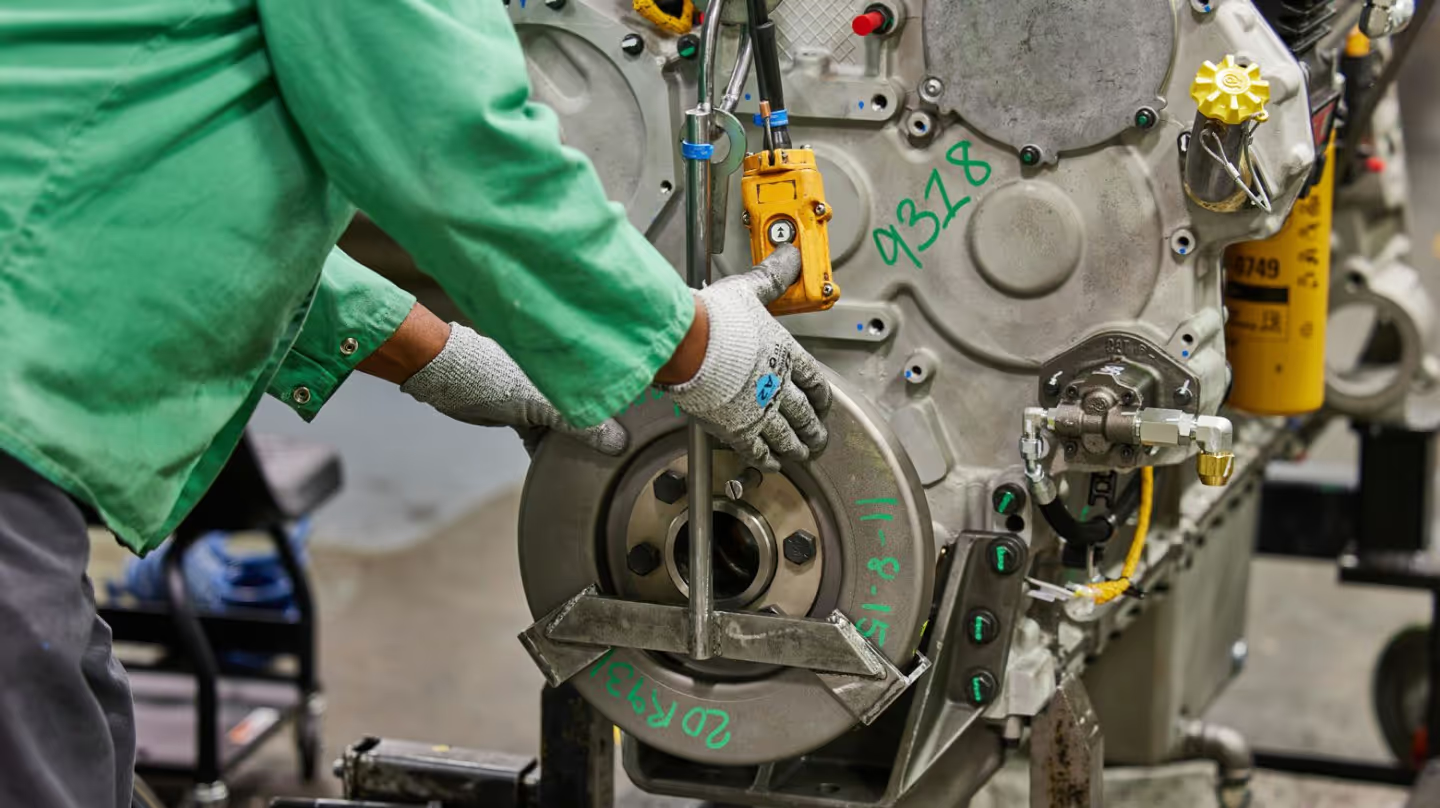
Why CAT Reman works
CAT Reman started in 1973 with a bold idea: that used diesel engines didn’t have to be scrapped. They could be returned, rebuilt, and resold – as good as new. At the time, this was revolutionary. Most equipment parts were replaced after just 120,000 miles. Caterpillar proposed an alternative: collect end-of-life parts, restore them to full functionality, and reintroduce them into the supply chain.
This was more than a technical fix. It was a shift in business model thinking. By encouraging core returns through refundable deposits, and committing to rigorous testing and quality control, CAT Reman created a system where customers saved money, dealers ensured faster service, and Caterpillar retained ownership of valuable materials.
Half a century later, the model is still growing.
Inside CAT Reman: Industrial-Grade Remanufacturing
When a used component arrives at a CAT Reman facility, the process is anything but simple. Each core is disassembled completely – every seal, gasket, and bolt removed. After a detailed inspection, parts that meet Caterpillar’s strict specs are salvaged. The rest are discarded or replaced.
What sets CAT Reman apart is the precision. Remanufactured components aren’t just cleaned or refurbished – they’re engineered to perform like new. In fact, many are updated with the latest design improvements before being reassembled. Engines are tested on dynamometers to verify full performance. The result is a part that delivers the same reliability as a brand-new one – often at half the cost.
With this level of detail, it’s no surprise that CAT Reman products come with the same 12-month warranty as new parts. Customers trust them. Dealers rely on them. And Caterpillar builds a second life into every product from the start.
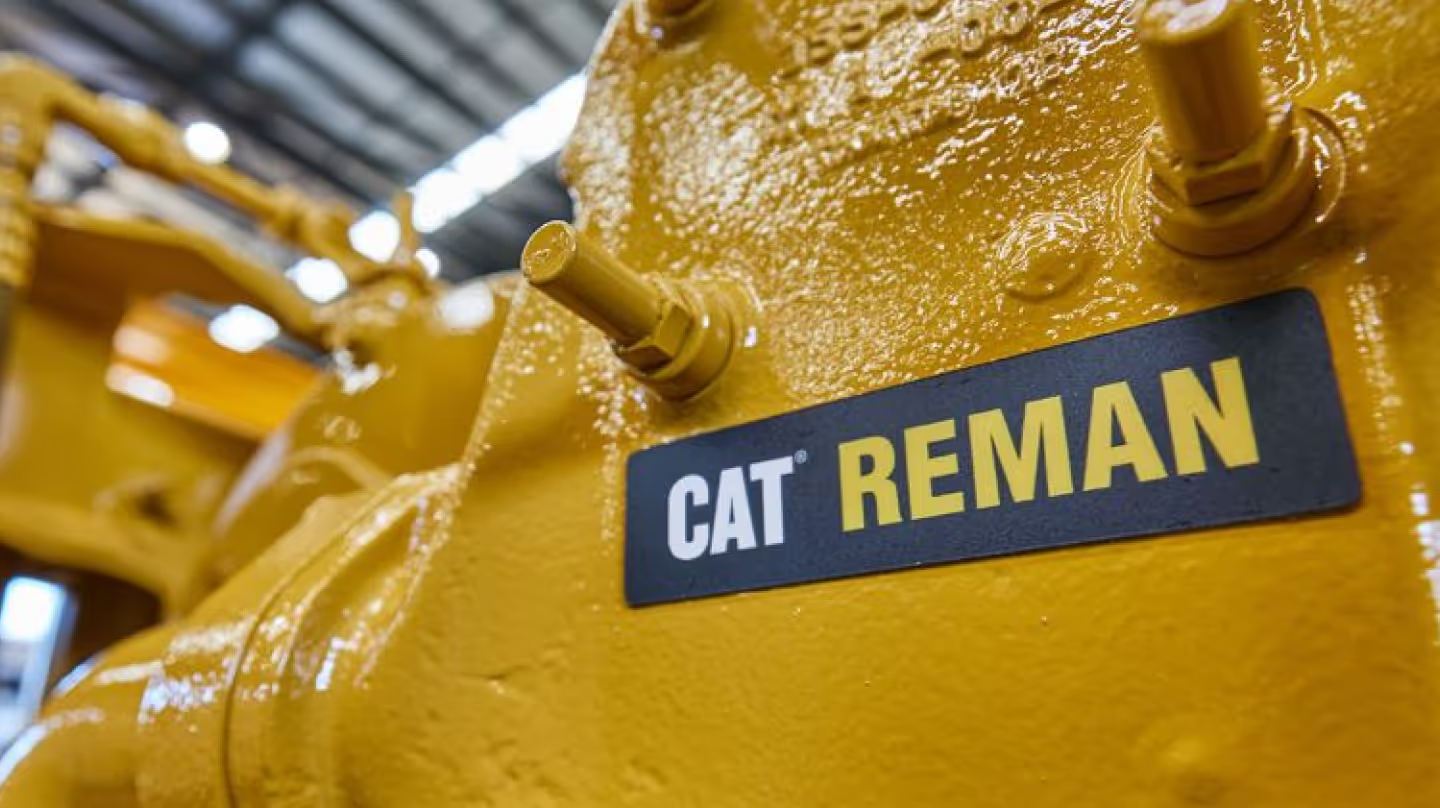
Building Circularity at Scale
CAT Reman’s success isn’t just about process – it’s about system design. The program is deeply embedded in Caterpillar’s global operations, with dedicated remanufacturing facilities across the U.S., Mexico, China, and Indonesia. This infrastructure allows Caterpillar to deliver fast, regionalized service while keeping transportation emissions low.
Just as important is the return incentive model. Customers pay a core deposit when purchasing a remanufactured part, refunded once they send the old one back. It’s a simple mechanism – but it works. Return rates are high, materials stay in the loop, and the system funds itself.
This closed-loop approach turns Caterpillar’s supply chain into a circular value engine. Products don’t just reach end-of-life – they cycle back, again and again.
Lessons for Other Manufacturers
CAT Reman isn’t just a case study in machinery. It’s a playbook for any company working with high-value components. Whether you manufacture appliances, tools, electronics, or industrial systems, the fundamentals remain the same: design for disassembly, incentivize returns, standardize reman workflows, and build trust in the second life of your products.
Crucially, Caterpillar has never treated remanufacturing as an afterthought. It’s a branded, engineered, and revenue-driving part of their portfolio. That’s what sets it apart – and what makes it replicable.
Looking Ahead
As Caterpillar expands into new product categories, CAT Reman will continue to grow alongside it. The company is already investing in new salvage technologies and exploring ways to digitally track parts throughout their lifecycle.
More than just a sustainability initiative, CAT Reman is becoming a core pillar of Caterpillar’s circular business strategy – helping reduce waste, cut emissions, and generate profitable secondary revenue streams.
How koorvi helps you build your own CAT Reman model
You don’t need Caterpillar’s global scale to start. But you do need a smart system. At koorvi, we help industrial and machinery brands launch and scale take-back and resale programs that are built to perform.
From automated portals to customer incentives, condition assessment to compliance – we provide the infrastructure for circular programs that drive value from returned machines. Because most companies leave money on the table after the first sale. We help you take it back.
Want to explore your circular potential?
FAQs
What is industrial remanufacturing and how does it work in heavy equipment?
Industrial remanufacturing is the process of restoring used machinery components to like-new condition through disassembly, inspection, replacement, and testing. In heavy equipment industries, this often includes engines, transmissions, and hydraulics. Programs like CAT Reman use advanced salvage techniques to meet the same quality and performance standards as new parts — while cutting costs and reducing waste.
Is remanufactured equipment as reliable as new machinery?
Yes — when done by original equipment manufacturers (OEMs) like Caterpillar, remanufactured parts are tested to meet the same performance specs as new components. Many reman products also come with full warranties and engineering upgrades. That makes them a reliable and cost-effective option for industrial operations.
What are the benefits of refurbishing heavy equipment components instead of replacing them?
Refurbishing machinery parts offers several benefits:
- Lower cost (up to 85% less than new parts)
- Faster turnaround (with ready-to-install components)
- Reduced downtime
- Lower environmental impact (less raw material and energy used)
Companies that refurbish engines or electronic modules often gain a competitive edge by reducing total cost of ownership.
How do core return systems work in industrial remanufacturing?
A core return system is a closed-loop process where customers return used components (called “cores”) in exchange for a deposit refund. This system ensures a steady flow of materials for remanufacturing while incentivizing customers to participate. It’s widely used in programs like CAT Reman and helps build circular supply chains in heavy industry.
What industries benefit most from remanufacturing and refurbishment?
Remanufacturing is especially valuable in sectors with high equipment costs and long product life cycles, such as:
- Construction and mining
- Agricultural machinery
- Transportation and logistics
- Power generation and heavy industry
Brands in these fields can reduce capital expenditures while meeting sustainability targets by integrating refurbishment into their service models.
How can manufacturers start a remanufacturing or trade-in program?
To start a remanufacturing or trade-in program, manufacturers need to:
- Identify high-value, high-return components (e.g. engines, motors, circuit boards)
- Design return incentives or deposit systems
- Set up inspection and refurbishment processes
- Ensure compliance with EPR and take-back regulations
- Use digital tools to manage logistics, tracking, and resale
Platforms like koorvi help brands build these systems from the ground up — with everything from customer-facing portals to backend logistics.